流程工业停机的实际成本
发布时间: 2023年07月19日
标签:
流程制造工厂面临着避免停机的巨大压力,因为这可能会严重影响企业的整体生产力、盈利能力和声誉。企业对计划外停机的原因和成本了解得越多,就能做更多的事情来帮助降低停机的发生率,并在停机发生时更好地做好应对准备。
图.石油炼化工厂(Pexels)
一.意外停机的主要原因
1.设备故障
设备故障无疑是意外停机的最常见原因。有些设备每天运行16—20小时,甚至全天候运行,从而增加了出现故障的可能性。大多数工厂对其最昂贵和最核心的机械设备给予了最多的保护,大型设备发生灾难性故障的情况相对较少。而旋转机械、阀门和管道等小部件的故障可能会导致停机和维修成本更高,而且发生的频率更高。
2.计划外的维护或修理
停机并不总是由于故障造成的。有时设备仍在工作,但没有按应有的方式运行。设备运行效率可能会下降,或者出现明显问题,例如噪音大、振动剧烈或温度急剧下降或上升。如果在计划的主要维护日之前关闭设备,则属于计划外停机,可能会影响生产力水平。
3.工人短缺
制造业维修人员的严重短缺,难以保证每台设备按时得到正确的维修。据德勤预测,到2030年,将有210万个技术岗位空缺。工厂里最有经验的员工大多快要退休或已经退休,然而,企业没有足够的训练有素的员工来填补空缺。
图. 设备维修人员(Pexels)
4.人为错误
简单的事故可能会以多种方式导致计划外停机。员工可能会在校准机械、配置产品组合等过程中犯错,也可能忽视泄漏和噪音上升等问题的早期迹象。由于缺乏经验丰富的员工,可能导致这个问题加剧。
二.意外停机的影响远比想象的要大
1.非计划停机导致高成本
计划外停机的主要影响首先体现在财务方面。当工厂宕机时,流程和生产都会陷入停顿,但工厂仍需承担成本,如给员工支付工资。公司也可能因生产损失错失利润,昂贵的原材料在等待生产重新启动时也可能会变质。
此外,工厂必须付费更换损坏的部件、支付额外的维护成本(包括员工加班),以恢复工厂的正常运行。如果导致停机的问题能够及时被发现,那么许多成本都是可以避免的。此外,许多工厂在停产后需要一段时间才能恢复全部生产力,并且可能需要丢弃前几批产品,直到产品质量恢复到所需水平。
据统计,每年《财富》全球500强(FG500)制造和工业企业因机器故障损失约330万小时的生产时间,因计划外停机损失近1万亿美元,造成的经济影响达8,640亿美元,占其年收入的8%。大型工厂平均每年损失323个生产小时,每小时损失532,000美元,即每年1.72亿美元。
生产计划的中断可能会导致工厂错过交货期限从而损害声誉,降低客户信心。这种情况在连续生产的工厂中尤其容易发生。
2.计划外停机影响员工士气
除了财务影响外,还有其他难以量化的影响。频繁的计划外停机会导致员工压力增加。他们会发现自己处于不利地位,因为大多数情况下他们只能处理紧急危机而不是主动预防危机。当员工陷入反应模式时,将很难跳出思维定势,为公司提出创造性的想法和解决方案。这将导致企业创新受到影响,从而影响未来的增长。
3.计划外停机可能会引发恶性循环
如果员工因反复遇到计划外停机而经常性处于恐慌状态,可能会引发恶性循环。恐慌会导致员工视野狭隘,不断犯简单的错误。有时,设备故障可能会引发恶性循环,维护团队或员工可能会使用错误的部件或不可靠的方法来尽快修复问题,从而改变流程节奏并导致不同的部件无法正常工作。
4.计划外停机会损害员工安全
大多数安全事故发生在瞬时操作期间,即工厂处于关闭过程中或关闭后重新启动期间。这些情况发生地越频繁,就越有可能导致安全问题。如果企业受到频繁停机的困扰,员工可能会决定继续在不安全的环境中工作,直到问题得到解决,以避免更长时间的停机。
三.减少意外停机影响的6种方法
1.预测性维护
预测性维护(PdM)使用工业物联网(IIoT)设备和传感器全天候监控工厂的运行情况;5G和边缘计算可实现将数据无延迟、实时共享到强大的分析平台;人工智能(AI)和机器学习(ML)分析可以理解大量数据,识别“正常”活动模式,并快速发现和识别重大异常情况。>>一文读懂工业设备预测性维护的概念与实现
有了这些信息,工厂工程师可以优化他们的维护计划,确保以最适当的时间间隔执行每一项检查任务,并且不会遗漏任何内容。德勤专家一致认为,“PdM是现有的最有效的维护策略,也是我们制定目标的黄金标准。”据统计,72%的大型工业企业受访者表示预测性维护是一个战略目标。
图.设备点检(全景网)
2.早期警报
除了确保在最佳时间检查和维护每台设备外,PdM还可以对即将发生的问题发出早期预警,以便在问题如滚雪球般蔓延之前将其处理。工程师可以通过对小问题进行快速修复来防止设备停机。但在其他时候,可能仍需要停止生产再进行设备维修,但维修可以在更短的时间内完成,从而将停机时间保持在最低限度。
借助早期警报,企业可以确认何时是进行维修或更换的最佳时间。若该问题尚不紧急,可以选择造成干扰最小的时间点进行维修,或将多个即将进行的维修合并到同一停机期间。这样一来,维护团队将有足够的准备时间来订购正确的零件,在等待备件到达前也不用延长停机时间。>>工业监控中如何解决告警疲劳的问题
3.自动化
使用人工智能和工业物联网的新工具可以实现许多工厂基本活动的自动化。这提高了员工的安全并加快了许多流程,同时还有助于降低人为犯错的风险。自动校准、配置和产品配方有助于防止可能导致停机的错误。
图.自动化生产(全景网)
4.跟踪停机时间
工厂经理可以使用先进的数据分析来跟踪每次生产停机事件,确定最常见的原因,并规划可在未来消除或减轻停机的解决方案。>>探索PreMaint中的三大工业运营工具:根因分析、过程优化和预测性维护
5.改善员工培训
如上所述,人为错误可能是导致意外停机的一个重要原因。提高员工培训水平有助于确保每个人都知道停机和启动时应遵循哪些安全预防措施、如何安全地进行维护、配置产品配方的正确步骤等。
6.数字孪生
数字孪生使用工业物联网、数据共享和机器学习来创建整个工厂的虚拟模型,该模型与物理工厂实时同步。工程师可以使用增强现实(AR)眼镜从任何角度“查看”工厂,即使他们不在现场。数字孪生提供了线上查看设备和重型机械内部结构的机会,在无需关闭整个生产流程的情况下,工程师可以检查设备、调查故障原因,甚至还可以通过数字孪生进行设备维修。除了帮助减少停机时间之外,数字孪生还有利于无法在现场办公的员工,可以作为留住想要退休或转向兼职工作的经验丰富的年长员工的解决方案。
四.不必忍受计划外停机
随着技术的发展,有许多新的方法来帮助企业重新获得对工厂的控制。PreMaint设备数字化解决方案,通过预测性维护,加上早期警报、数字孪生、根因分析工具和不断提高自动化程度的工具,可以减少工厂计划外停机的频率和影响,从而提高整个系统的生产和盈利能力。
来源:翻译自网络,如有侵权,请联系删改。
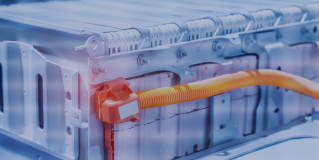
获取PreMaint设备数字化解决方案
延展阅读
>>设备健康管理系统PreMaint可以实现更智能的预防性维护
<更多信息可关注公众号“设备工程”获取>